
Characterising offset printability
Simulating or predicting offset printability of papers using appropriate tools
- Simulating mottling phenomena
- Studying picking parameters
- Characterising ink set-off and drying time
- Measuring ink gloss
Generate Value...
The offset printing process (viscous ink, paper dampening, high machine speed, etc.) is liable to generate defects resulting in claims or the downgrading of papers and printed substrates.
Implementing specific suitable tests going beyond standard laboratory equipment provides a means of:
- Predicting the compliance of papers for this market,
- Analysing and proposing solutions to phenomena observed during industrial printing:
* Changing paper, its composition
* Changing print parameters (ink, dampening solution, etc.)
The CTP has been developing expertise and laboratory facilities tailored to offset printing management for more than 40 years.
Observing printed media forming the subject of a claim
Context and performance
A papermaker, a printer and a publisher come across a printing problem. It is difficult to understand, and the client wishes to establish the cause of the defect, know whether the defect is specific to this paper or another one, whether the unevenness observed is due to the paper, etc.
All the causes of a printability issue in industrial conditions (Sheetfed Offset, HeatSet or ColdSet Web Offset , QuickSet Offset) can be investigated in the laboratory.
Any printability issue can be submitted, even the design of a new device.
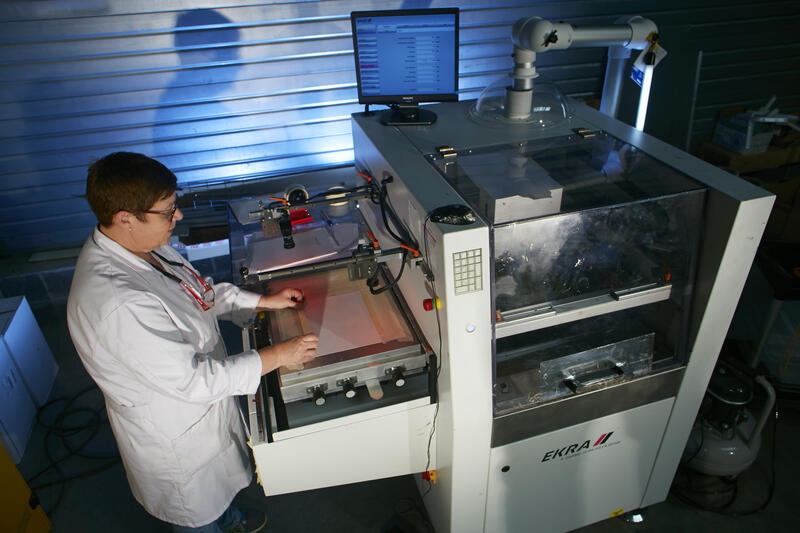
Printing in the laboratory
Content of services
Receipt of control samples.
Analysis of the situation and proposal of appropriate tests, liaising with the client.
Choice of test, setting-up to print a solid block on an IGT printability tester at constant speed, or printing with an initial dampening stage and a second industrial ink transfer stage with a blanket-covered disk, either on an IGT tester or a Prüfbau tester.
In the case of drying speed: lab printing in conditions as representative as possible, followed by simulation tests, such as Wallace abrasion or automatic set-off with special device named MEP.
Assessing ink drying on a special automatic set-off testing instrument
Deliverables
- Implementation of printing tests
- Characterisation, assessment
- Report and interpretations as requested.